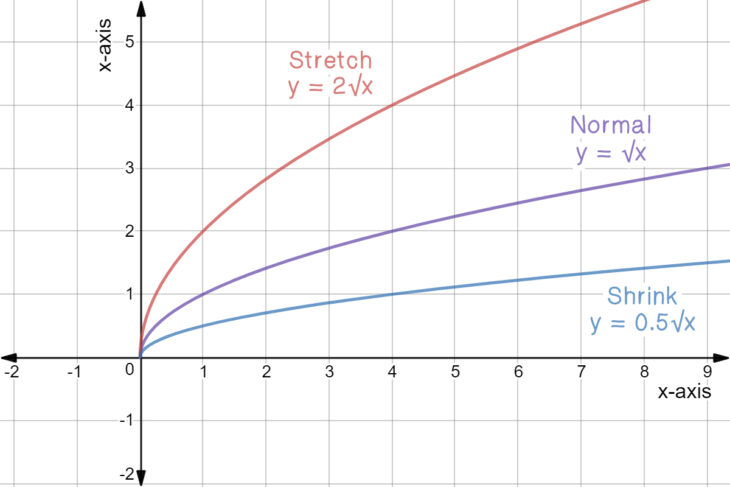
The Importance of Sensor Recalibration
In today’s tech world a lot of things are operated by sensors. Those that we all know too god are the car sensors that have given all of us trouble from time to time.
A sensor is a device that emits some kind of signal to sense a physical phenomenon. A sensor, in the broadest sense, is a device, module, machine, or subsystem capable of detecting events or changes in the environment it is positioned in and then transmitting that information to other electronics for processing.
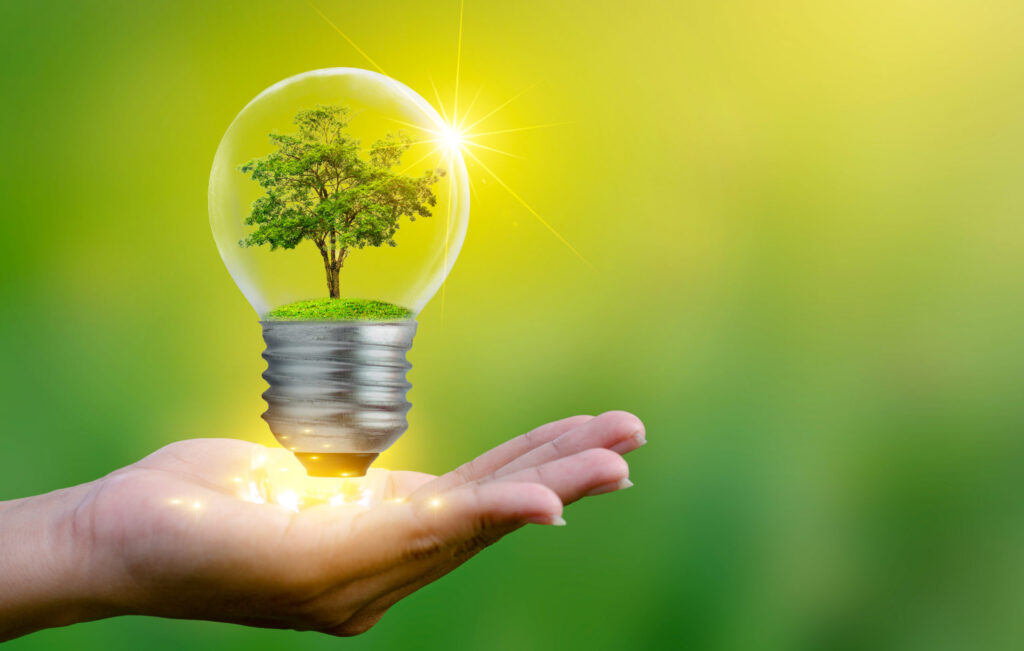
Now, when we know this, we then can deduce that after some time, due to the impact of the environment, or other factors these sensors tend to go bad, right? Now some get bad to the point that we have to replace them, while others that have a calibration capability need to be calibrated to continue their normal function. Today we are discussing this topic and we will try to explain to you what a sensor calibration is important and why you should do it as soon as you get misreads or error reports, especially on the readings you did not have issues with before this.
Now we mentioned that there are a lot of different sensors and they can be located in many different devices. One of the devices that use sensors, and we need to mention it since not a lot of you know this, is the UV lamp. Just like any other device, it can go bad, sensors can lose values and you need to do a UV light repair.
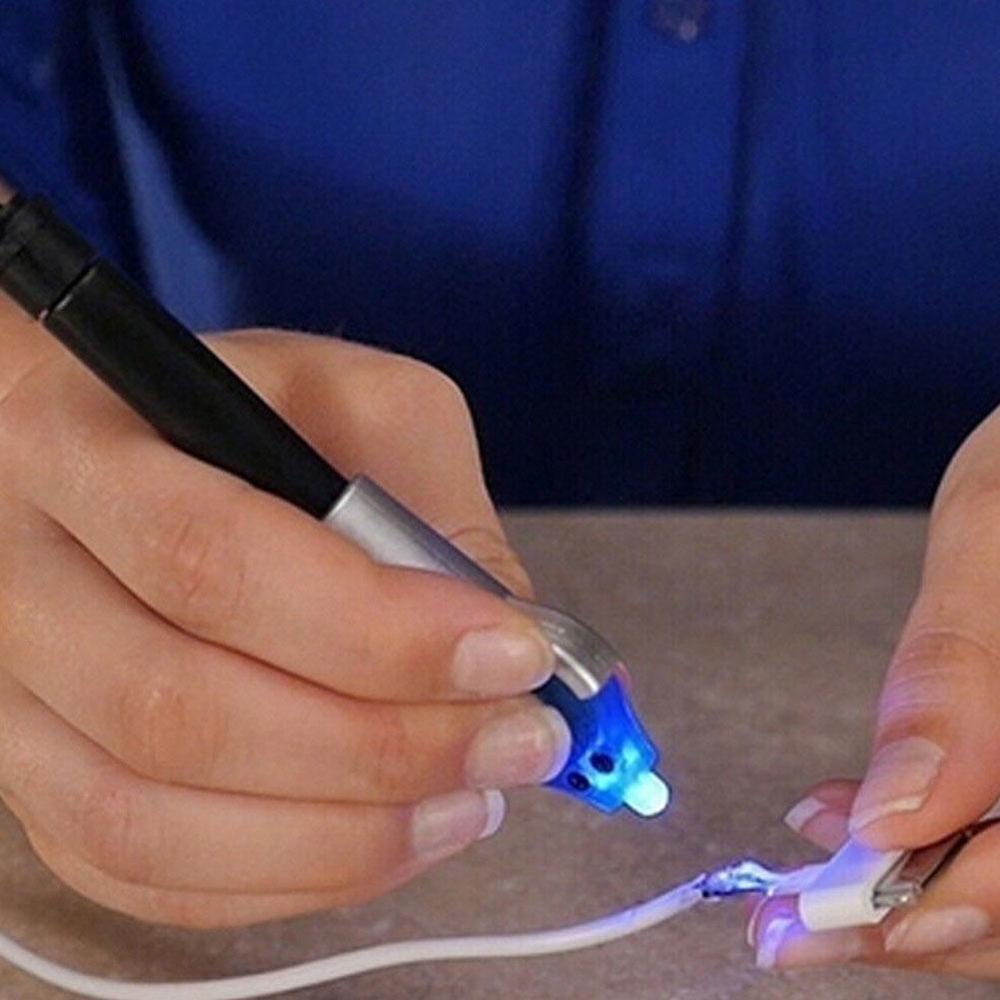
Continuing to the topic, let’s try and explain why sensor calibration is crucial and when it should be conducted. When engineers build anything that works with a lot of data these days, they incorporate sensors to monitor critical process parameters. These readings are used to assist the monitoring and control system in regulating things so that everything runs as smoothly as possible and that the required values and safe operation are retained. If you’re wondering how the functioning of all these sensors guarantees that the process’s actual value is read and the data is sent to the control data or module, the response is — because of sensor recalibration!
Before we dive into sensor recalibration, we must state one more time that there are a lot of different sensors and some of them can be recalibrated while others can’t. Depending on the usage of the sensor it can be pre-calibrated for you from the plant or it can be uncalibrated and left to you to do this thing. The sensor that does can’t be calibrated are usually those that are already calibrated for a certain task and they are your plug-and-play sensors. Examples of those are car sensors for temperature, oil levels, and heat, sensors for the exhaust gasses, and so on. These cannot be recalibrated and as soon as they start to act up and cause issues in your vehicle, they are replaced with a new one that comes calibrated for your vehicle specs, you just have to plug it in the system.
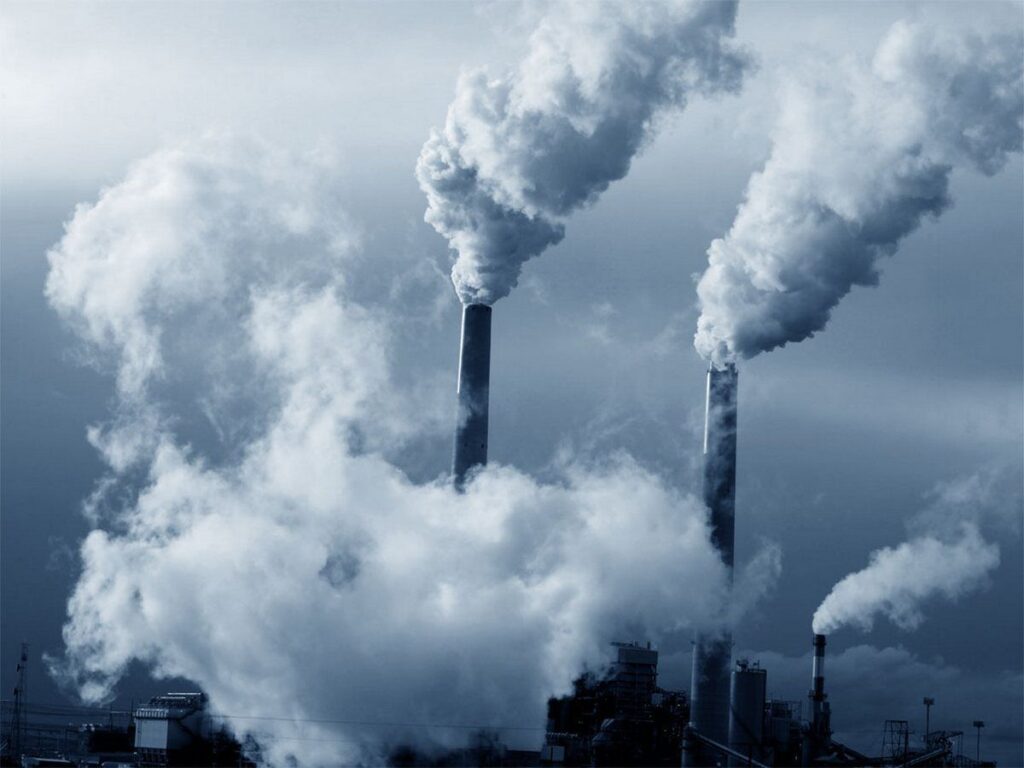
- Let’s talk about the ones that can be re-calibrated now. Sensor recalibration is an adjustment or series of changes made to a sensor or instrument to ensure that it operates as precisely and without errors as feasible. An algebraic disparity between the indication and the actual value of the measured variable is an error in sensor data. Sensor measurement errors can be generated by a variety of circumstances.
- A sensor value error can be caused by a lack of a sufficient zero reference. Modern sensors and transmitters are electronic devices, and their reference voltage or signal may drift over time as a result of factors such as heat, pressure, humidity, or abrupt changes in the environment.
- The range of sensors may also alter as a result of the identical situations we just mentioned. Changes in the operating range of the process can also have an impact, so you must be cautious.
- A sensor measurement error can occur owing to mechanical wear or damage, although this form of error usually necessitates the repair or replacement of the equipment.
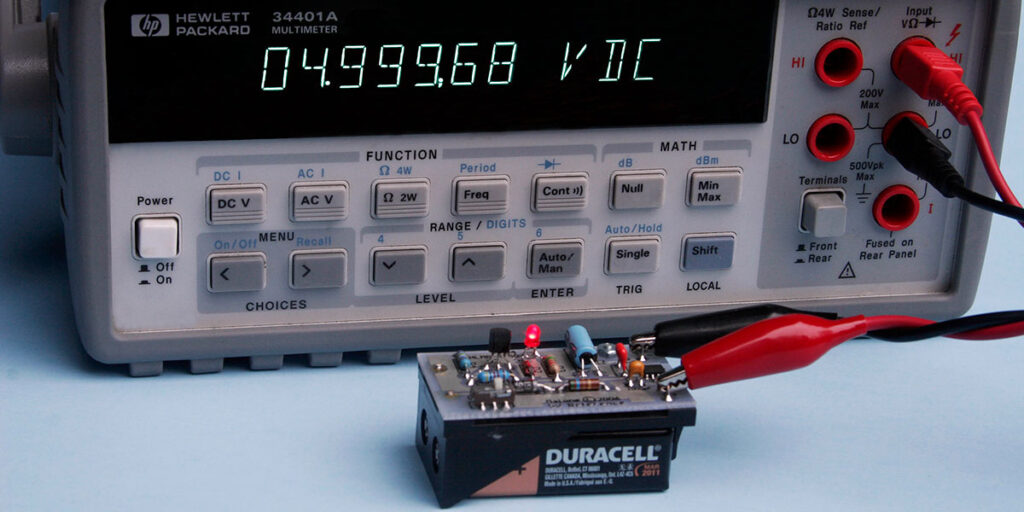
Overall, sensor mistakes are undesirable since the control system will lack correct data from which to make regulated judgments if they occur. Process safety may be jeopardized if sensor calibration deviates too far from accurate process conditions.
Every instrument in anything must function well and with adequate calibration to produce accurate data, which allows for good process control. When proper control is achieved, the entire process or operation has the highest chance of running smoothly and safely.
Periodical calibration is required for most sensors, especially those that can be calibrated and recalibrated. This means that after a particular length of time, sequences, or operations in any process or operation, a specific sensor in the entire system must be recalibrated to ensure correct functioning and reliable data return.
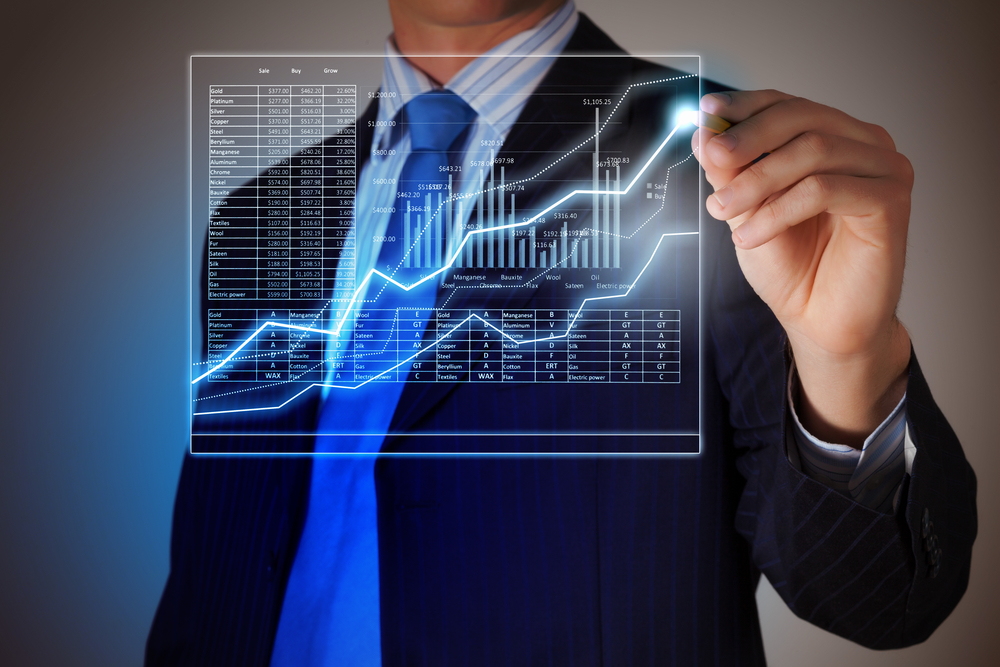
Depending on the sensors and their placement, type of operation, and span, they can be hard or easy to recalibrate. This is why experts always advise a check of the sensors’ output data before the recalibration. This is the way you make sure that the sensor needs, or doesn’t need, any adjustments. If you have the data of the ideal values then you can put them against the values that your sensor is outputting. If the measured values deviate too much from the ideal values your sensor is ripe for recalibration or replacement, depending on the type.
If the values of deviations are in the less than maximum allowed range then a sensor calibration is not needed. This test before calibration is much appreciated since it allows you to check the actual sensor and stops you from recalibrating something that is still operating within the allowed error line. As we already said, some sensors are hard to locate and reach which can prolong the calibration process. This test will both save you time, money, and effort.