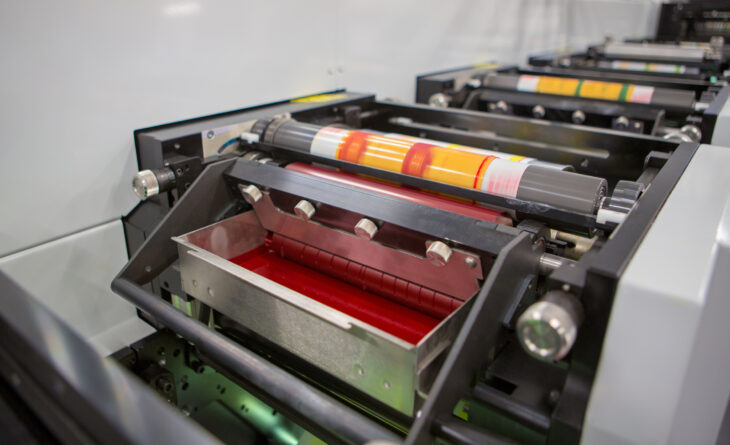
What Is Flexographic Printing?
In the dynamic world of printing, flexographic printing stands out as a cornerstone. What is flexo printing process? It’s a versatile, high-speed method that is pivotal in the printing industry, especially in packaging. This article delves into the intricate workings of flexographic printing, tracing its historical roots and exploring its technological advancements.
Historical Background
Flexographic printing, originally known as ‘Aniline printing’ due to its use of aniline oil-based inks, has a rich history. Its origins date back to the early 20th century. Initially, it was a rudimentary process, mostly used for simple labeling and packaging. However, over the decades, flexography evolved remarkably, adapting to new challenges and technological breakthroughs, transforming into the sophisticated process we see today.
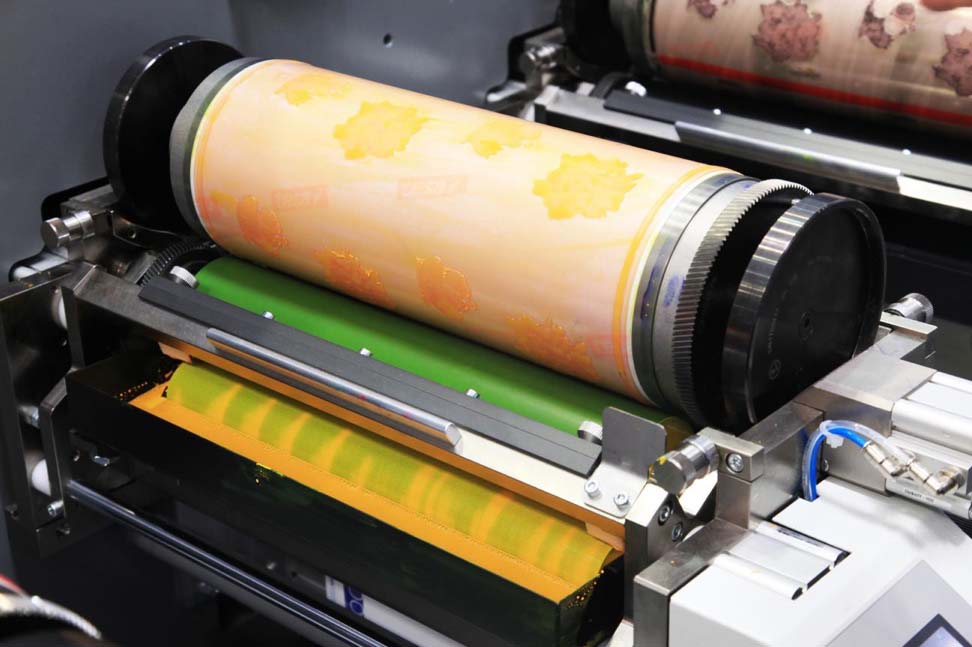
The Flexographic Printing Process
Flexographic printing, often referred to as ‘flexo’, is a method steeped in innovation, efficiency, and versatility. This section delves into the intricacies of the flexographic printing process, explaining its key components and their roles in producing high-quality prints.
Prepress process:
- Artwork and design. The journey begins with the creation of a graphic design. This design is then translated into a digital format, which is essential for creating the printing plates.
- Plate making. Using the digital artwork, photopolymer plates are created. These plates are made light-sensitive, and the image is etched onto them using a controlled light exposure process. Each color in the design requires a separate plate.
Printing components:
- Plates. The heart of flexographic printing, these flexible plates are attached to rotating cylinders. The raised images on these plates are what transfer the ink onto the substrate.
- Anilox rollers. These are metal or ceramic rollers engraved with thousands of tiny cells. They pick up ink from the ink chamber and transfer it to the printing plates in a controlled and consistent manner.
- Ink system. Flexographic printing uses a range of inks, from water-based to UV-curable inks, depending on the substrate and the end-use of the product. The ink must be of a specific viscosity to ensure proper transfer and drying.
- Substrate feed. The substrate, which could be paper, plastic, foil, or other material, is fed into the printer and passes through each printing station. Each station applies a different color, building up the final image.
Printing process:
- Ink transfer. The anilox roller applies ink to the printing plate. The raised areas of the plate pick up the ink.
- Printing and drying. The plate then presses against the substrate, transferring the image. Each color is applied in a separate pass, with drying processes in between to prevent smudging.
- Quality control. Throughout the printing, quality control is critical. Modern flexo printers often have cameras and sensors to monitor the print quality, ensuring consistency and accuracy.
Post-press and finishing:
- Cutting and folding. After printing, the substrate may be cut, folded, or shaped as per the requirements of the product.
- Lamination and coating. Additional treatments like lamination or UV coating may be applied for added durability or aesthetic effect.
- Inspection and packaging. The final products are inspected for quality, packaged, and prepared for shipment.
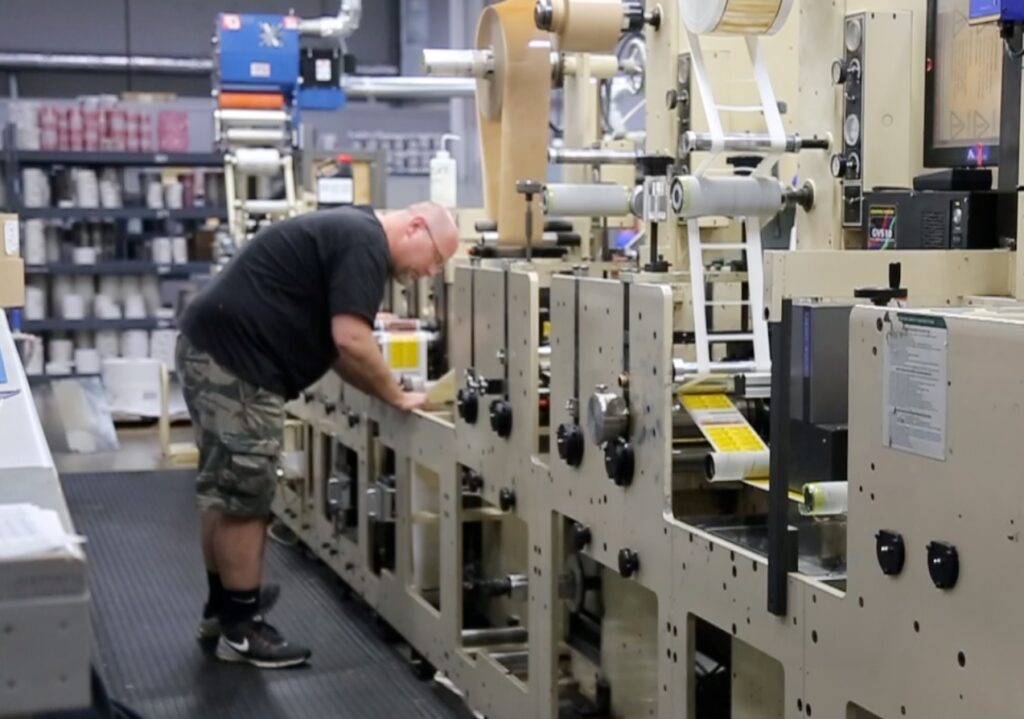
Technological Advancements
Technological innovation has been a driving force in flexography’s evolution. The introduction of digital plate-making has drastically improved image quality and printing efficiency. Digital technology in flexography allows for precise color matching, faster production times, and more detailed graphic capabilities. It’s this synergy of tradition and technology that keeps flexographic printing at the forefront of packaging solutions.
Advantages of Flexographic Printing
Flexography’s popularity in packaging is largely due to its speed and efficiency. The ability to print large volumes quickly makes it ideal for high-demand products. Moreover, its versatility in handling various inks and materials allows for a broad range of packaging applications. Notably, the durability and quality of flexographic printing ensure that products stand out on the shelves, combining aesthetic appeal with practicality.
Applications of Flexographic Printing
What is flexographic printing used for? Its applications are extensive and diverse, marking its presence in various industries. Primarily, it’s renowned in the packaging sector for printing on materials like plastic bags, food packaging, and wallpapers. In the label market, flexography is the go-to method for high-quality, durable labels, which are resistant to fading and wear. Additionally, it’s utilized in printing newspapers and magazines, where speed and efficiency are paramount.
Examples of products include:
- Food packaging. Everything from snack bags to beverage cartons.
- Labels. Durable labels for consumer goods like shampoos, detergents, and more.
- Wallpapers and gift wraps. Vibrant prints and patterns.
Environmental Considerations
Sustainability is increasingly becoming a priority in the printing industry. Flexographic printing has adapted to this by:
- Eco-friendly inks. Transitioning to water-based and UV-curable inks, which are less harmful to the environment.
- Recycling and waste reduction. Implementing processes to recycle materials and reduce waste.
- Energy efficiency. Advancements in equipment to reduce energy consumption.
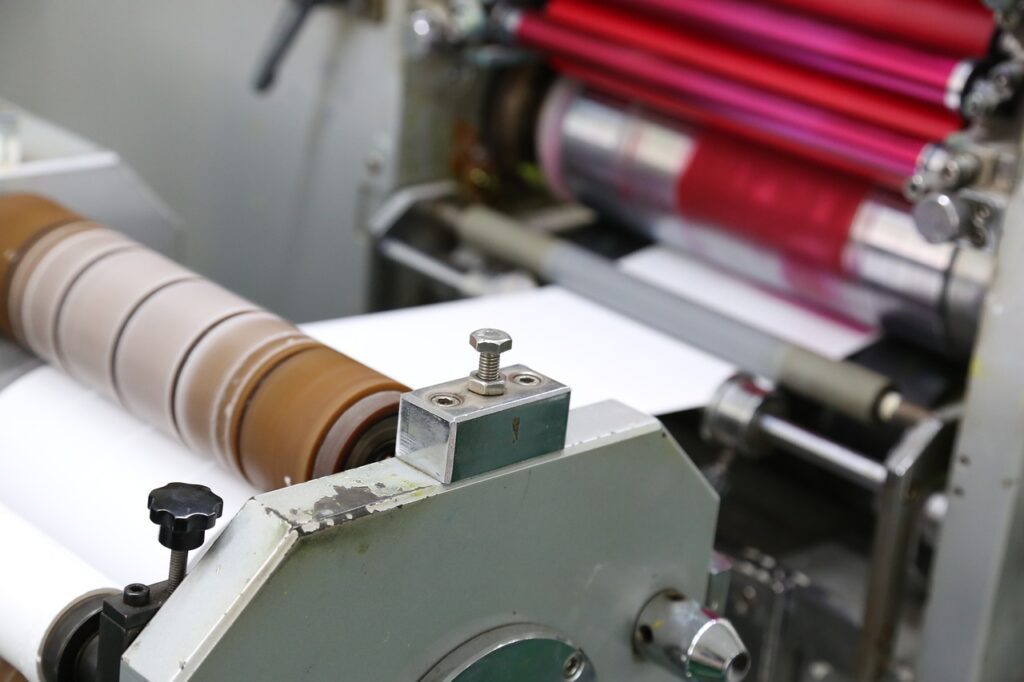
Comparison with Other Printing Techniques
Flexographic printing holds its unique place in comparison to other techniques like offset printing. While offset is known for its high-quality and cost-effectiveness for large volumes, flexography stands out for its versatility and speed, especially on non-standard materials. It’s the preferred choice for high-quality packaging and labeling due to these factors.
For a deeper insight into how flexographic and offset printing compare, you can read the article “Offset vs Flexo Printing“.
Future of Flexographic Printing
Looking ahead, the future of flexographic printing seems bright and promising. Innovations in digital technology, sustainable practices, and material science are expected to drive its growth. The trend towards more personalized and environmentally friendly packaging will likely spur further advancements in this field.
Conclusion
Flexographic printing, with its versatility, speed, and adaptability, continues to be a pivotal player in the printing industry. Its role in package and label printing underscores its importance. As we move towards a more digital and sustainable future, flexographic printing is poised to evolve and maintain its relevance in the industry. The journey of flexography, from its humble beginnings to a modern-day printing powerhouse, is a testament to its resilience and capacity for innovation.