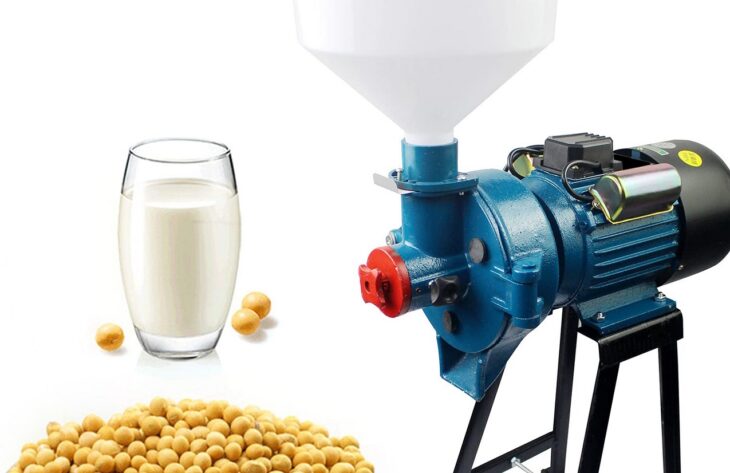
What is a Wet Grinding Process? Method Overview
In the multifaceted domain of material preprocessing, the wet grinding process carves a niche for itself due to its proficiency in reducing particle size, which is imperative for a multitude of applications across various industries. This article aims to elucidate the methodology and the substantial benefits embedded in the wet grinding process.
Unraveling the Essence of Wet Milling Method
Wet grinding, synonymous with wet milling, is a process characterized by the reduction of particle size facilitated by a liquid medium. This distinct feature differentiates it from dry grinding, where mechanical force is solely responsible for size reduction. The liquid medium not only aids in the processing but also manages the heat generated, ensuring the integrity of the material being processed.
Key Components of Wet Grinding
- Liquid Medium: The choice of liquid, ranging from water to various solvent systems, is crucial as it acts as a coolant, minimizing undesirable thermal effects.
- Grinding Equipment: The machinery employed, be it ball or bead mills, play a pivotal role in ensuring the effectiveness of the material pre-treatment.
- Material Input: The nature of the material to be ground significantly influences the process, determining factors like the duration of grinding and the choice of liquid medium.
Delving into the Wet Milling Process
Wet milling excels in both size reduction and the separation of components within a material. The liquid medium facilitates the separation of the milled components, which is exceptionally beneficial in industries such as food processing, pharmaceuticals, and ceramics.
Steps
- Initial Size Reduction: The material is first subjected to size reduction to create smaller particles.
- Separation: The liquid medium aids in separating the desired components from the undesired ones.
- Collection: The separated components are then collected for further processing or usage.
Embracing the Wet Ball Milling Process
Wet grinding is a robust and efficient method which employs a ball mill to reduce the particle size of materials. The latter, loaded with grinding media like steel balls, facilitates a homogeneous slurry when the material and water are fed into it.
Variables in Wet Ball Milling
- Ball Size: The size of the balls impacts the fineness of the resulting particles.
- Mill Speed: The speed of the machines influences the grinding efficiency.
- Milling Duration: The length of the process affects the particle size and quality.
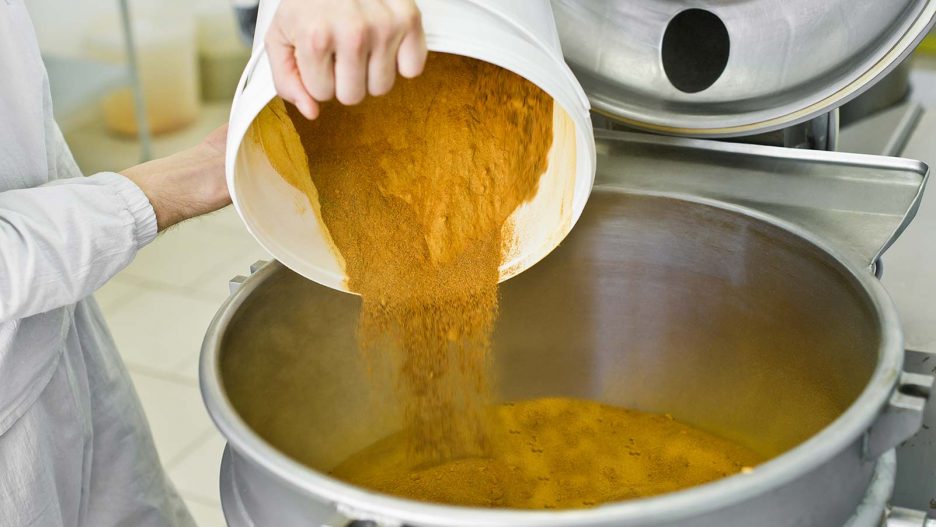
Benefits and Applications
The advantages of the wet grinding process extend beyond mere size reduction, leading to enhanced material properties and a wide range of applications.
Benefits
- Enhanced Reactivity: Improved particle surface area and reactivity.
- Optimized Rheological Properties: Better flow characteristics of the material.
- Reduced Thermal Stress: The liquid medium manages the heat generated, preventing thermal degradation.
Applications
The applications extend across various industries, enhancing product quality and manufacturing efficiency. Some of the industries that benefit from wet grinding include:
- Battery Production: Enhancing cell production and stability.
- Ceramics: Producing finer ceramic powder.
- Pharmaceuticals: Achieving nanometer fineness for drug formulations.
- Food Processing: Ensuring consistent food processing.
- Cosmetics: Creating unique chemical combinations for cosmetic products.
- Chemicals: Forming different chemical combinations.
- Paper: Producing thermal-sensitive paper.
- Inks & Paints: Achieving desired consistency.
- Coatings: Breaking down strong particle bonds for different coatings.
- MLCC/LTCC and Pesticide Production: Creating more conductive materials for electrical components​​.
Each of these industries leverages the wet grinding process to enhance particle fineness, material consistency, and overall product quality.
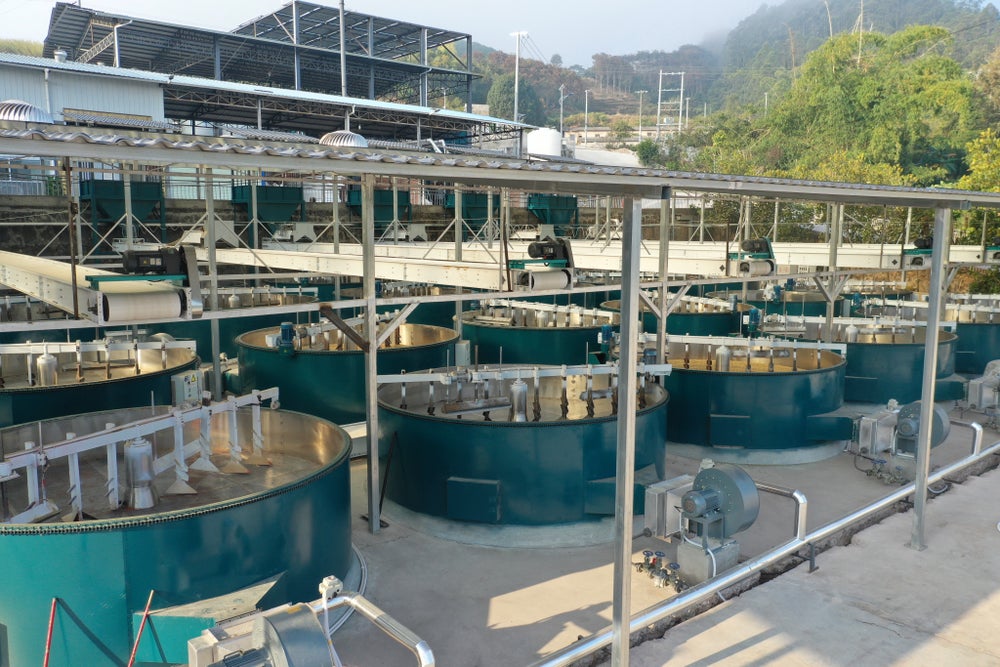
Key Considerations
- Equipment Choice: Selecting suitable machinery for the wet milling process.
- Process Design: Designing the process to meet the desired outcomes.
- Liquid Medium Selection: Choosing an appropriate liquid medium to facilitate separation and grinding.
Equipment for Wet Milling by Allwin Manufacturer
Allwin, a notable manufacturer in the grinding and dispersing machinery realm, offers a range of wet grinding dispersion equipment meticulously designed for producing mixtures of exceptional homogeneity:
- Bead Mill: Utilizes grinding beads to facilitate consistent grinding.
- Disperser: Powerful mixer designed to break and disperse processed materials efficiently.
- Auxiliary Machinery: Enhances machine performance, ensuring safer operations.
- Tank: Contains the liquid mixture, made with durable steel to endure corrosion and extreme temperatures.
- Grinding Media: Features excellent impact, corrosion, and abrasion resistance, making zirconia bead an ideal choice.
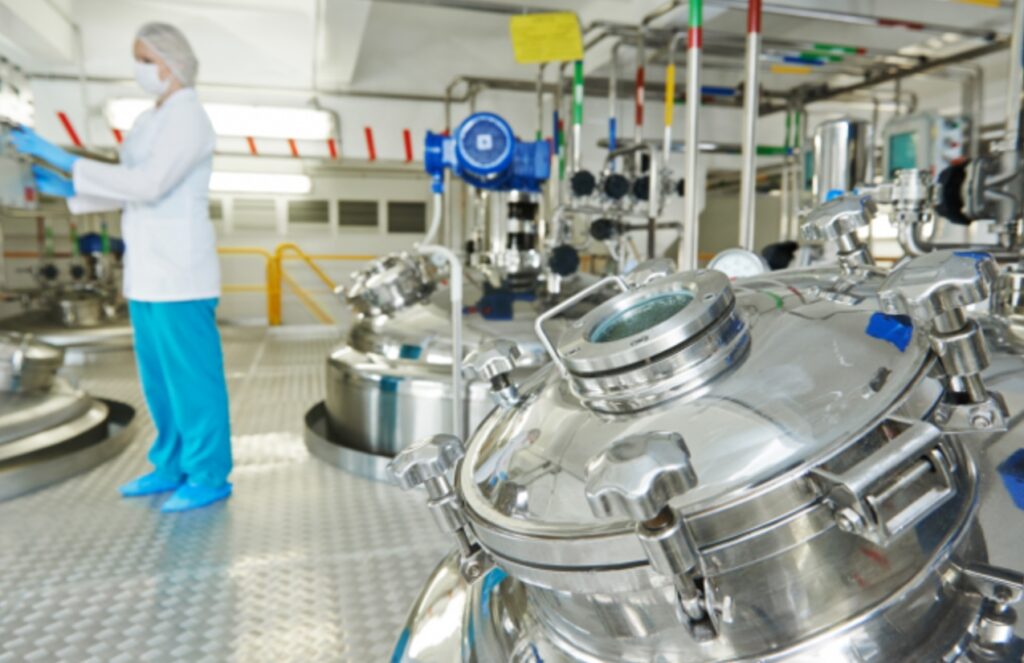
Wrapping Up
The wet grinding process, with its various methodologies including wet milling and wet ball milling, emerges as a cornerstone in modern material processing industries. Its ability to deliver precise particle sizes while preserving material characteristics makes it an indispensable tool in contemporary industrial practices. The thorough understanding and appropriate application of wet grinding and its numerous methods can significantly enhance the quality and functionality of products, heralding a new era in material science and engineering.