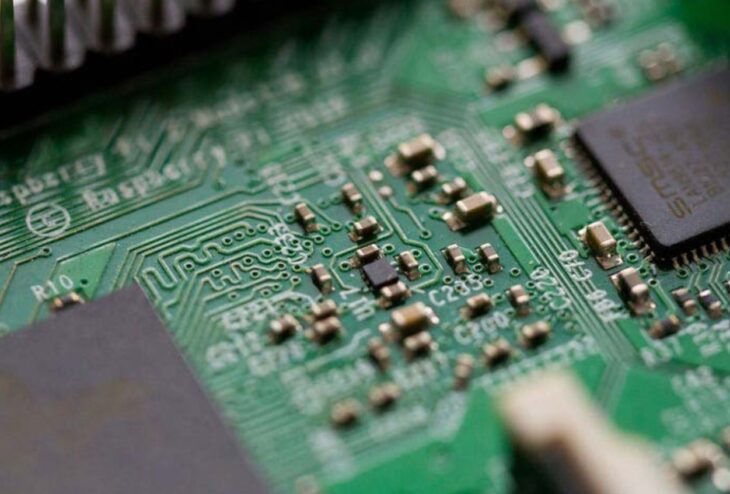
How Product Designers Use Parylene Coating
Parylene coating stands front and center when it comes to coatings that are conformant in nature. This makes it the top choice for most product designers and manufacturers. This won’t come as a surprise for people handling parylene on a day to day basis. However, its uses and the exact application method may not be known to people who don’t deal with it on a daily basis.
The polymer truly surpasses several other materials in the category with its easy application and high performance. Parylene is a highly versatile polymer coating that has become popular in several industrial settings. The name is in fact a generic term for a unique polymer series based on paraxylene. Read more to learn about parylene.
Parylene Application Process
Parylene coating is applied using specialized vacuum deposition equipment at ambient temperatures. The deposition takes place at the substance’s molecular level. This is where the coating essentially grows a molecule film one at a time.
The first step is the heating of dimer, a solid and granular raw material, which is heated vacuum heated and vaporized using dimeric gas. The next step involves pyrolization of the dimer to cleave it back to its monomeric form. This monomer gas is then deposited on the targeted surface in a room temperature deposition chamber. The gas is coated as a thin and transparent polymer film.
Parylene coating effortlessly penetrates all tight areas and crevices because it is applied as a gas. This is true for multi-layer components which can be coated uniformly providing complete encapsulation. Optimal thickness of the coating is based on the coating property desired and the application.
Typical thickness of parylene coating is measured in microns even though the coating can range in hundreds of angstroms to several mils of thickness.
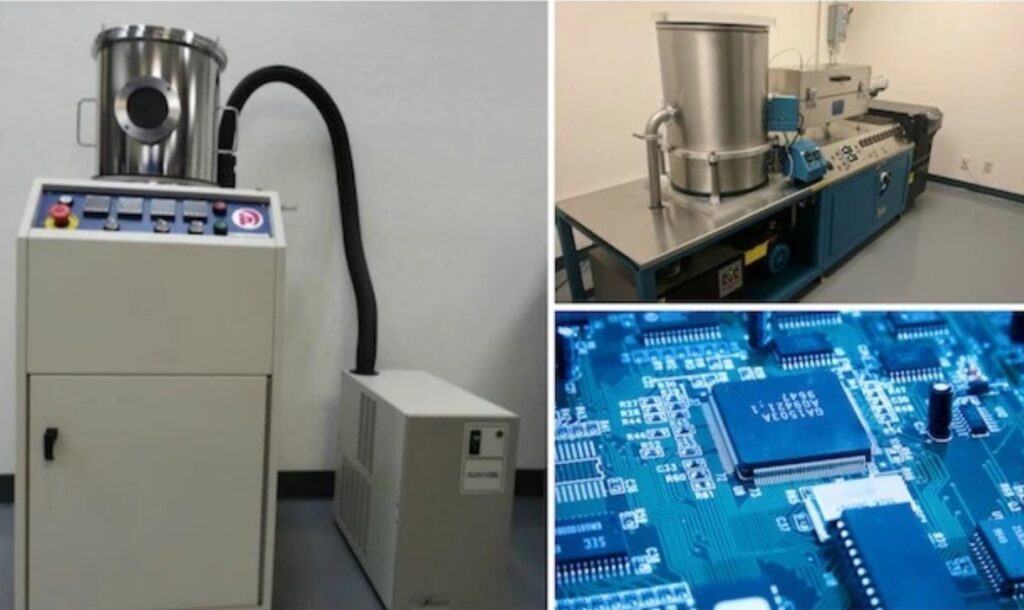
Variables Influencing the Parylene Coating Process
There are two general parts to the parylene deposition process. The first is the science that is explained in detail above. The second is the art of application. Parylene coating will only come out as it is supposed to when applied by specialists who have the right expertise and insight honed over the years. The coating’s performance and protection capabilities need to be consistently and fully realized.
The art of parylene coating includes thoroughly understanding the various variables which can affect the performance of the coating. Working with the various factors eventually affects the success of the coating application. Vapor deposited parylene coatings tend to conform and reach surfaces that are generally unreachable by liquid coating.
Vapor deposition process allows for the production of a thin film that uniformly grows on the surface. This takes place one molecule at a time. Liquid conformal coating, when applied by dipping or spraying can collect and pool within low crevices. It’s vital to steer clear of sharp points and raised edges. Pinholes, cracking, bubbling, and orange peel are usually common with liquid coatings.
Optimal Adhesion to Substrate Material
Parylene can be applied to a wide variety of substrates. This includes elastomer, plastic, metal, paper and glass. Adhesion is usually achieved by treating the material with A-174 silane before applying the parylene coating. There are few highly polished polymeric substrates and metallic substrates that usually present a challenge to parylene coating.
However, the right application expert can manage parylene applications on the most resistant surfaces with ease. There are several new adhesion promotion technologies which can solve a wide variety of these challenges posed.
Substrate Cleanliness is Important
Proper parylene adhesion can only be achieved when the substrate is cleaned properly. Manufacturing oils, particulates, other materials, and human oils will affect parylene adhesion. These materials are not considered to be a viable component to parylene reliability and performance. It’s critical to work with a product designer that has widely accepted processes and standards for working within a clean and sterile room.
Substrate Preparation for Effective Parylene Coating
Parylene can be easily used to coat any type of surface. This includes deep crevices and multi-layers. All surfaces within the deposition chamber tend to get coated with Parylene without any problem. However, this is true only if the technicians are careful not to mask the intended area.
Product designers work with a large bank of masking and fixturing techniques to minimize contact points. They avoid coating on areas that don’t need to be coated.
Applications of Parylene Coating
Parylene is a highly versatile polymer coating with widespread applications. Few of the more notable areas include:
-
Medical Industry
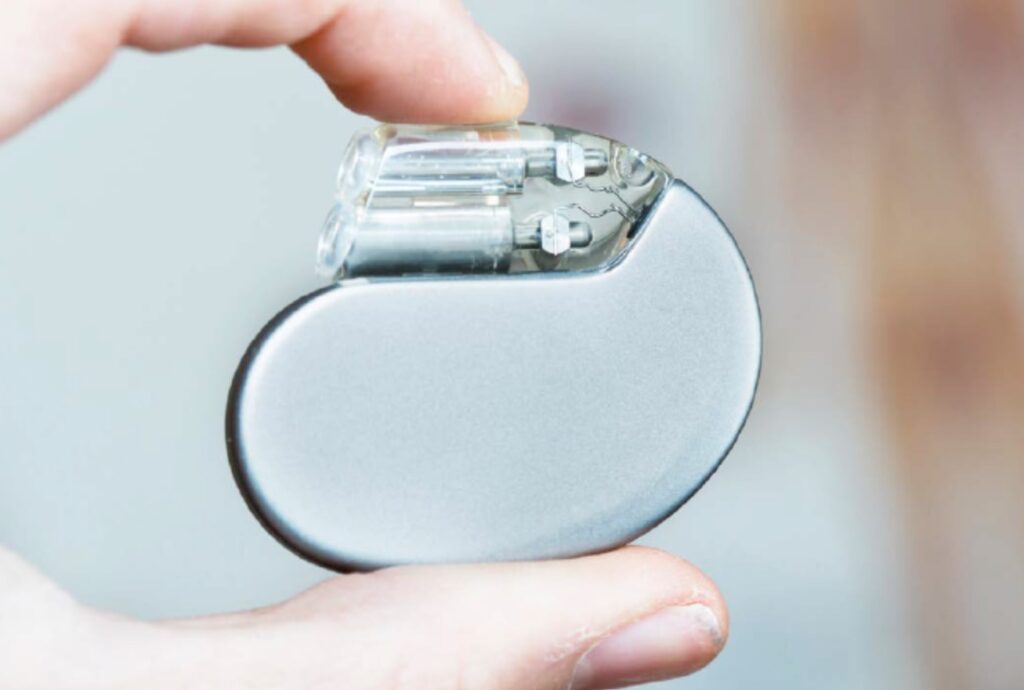
Parylene has the most widespread use in the medical industry. The coating is non-toxic, biocompatible and pinhole-free. It provides protection as a barrier against both inorganic and organic solvents and fluids. The polymer can also withstand several different methods of sterilization, including autoclave, gamma, and E-beam.
Few examples of parylene coating within the medical industry include coronary stents, hypo needles, hearing aids, implantable devices, catheters, and medicine bottles.
-
Automotive Industry
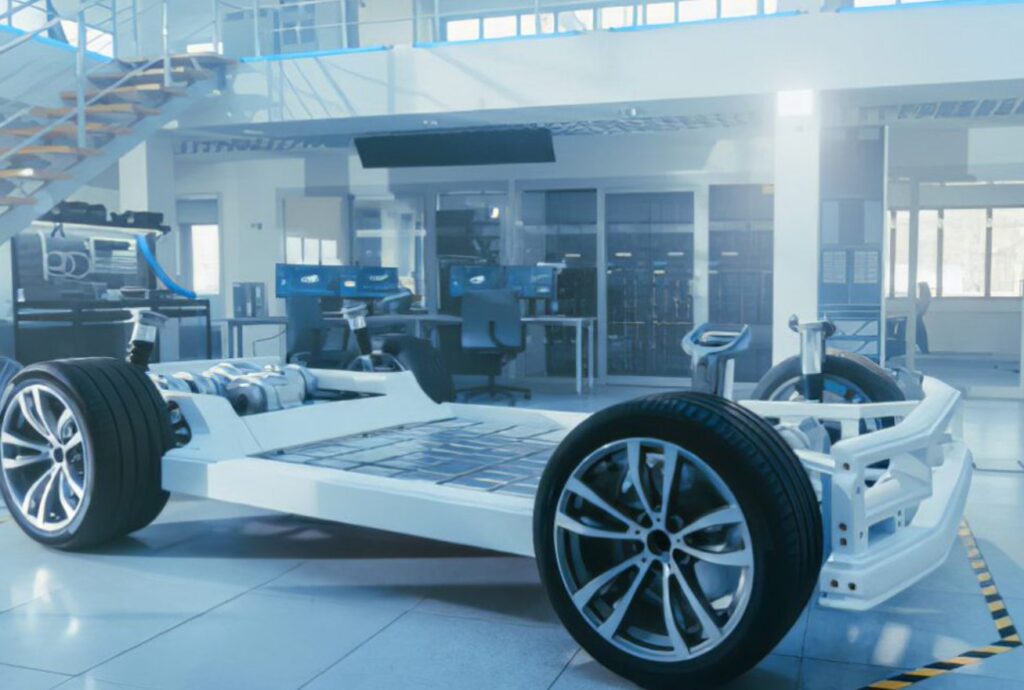
This industry also uses parylene extensively. Vehicles have complex electronics systems and components that require specialized protection since they operate within harsh environments. They are exposed to heat, solvents, oil, cold, and salt. Parylene can effectively adhere to almost every surface in the vehicle while penetrating every cranny and nook.
This makes it an ideal coating for computerized components and sensors. The polymer is usually found on seals, gaskets, circuit boards, pressure sensors, and power systems.
-
Space
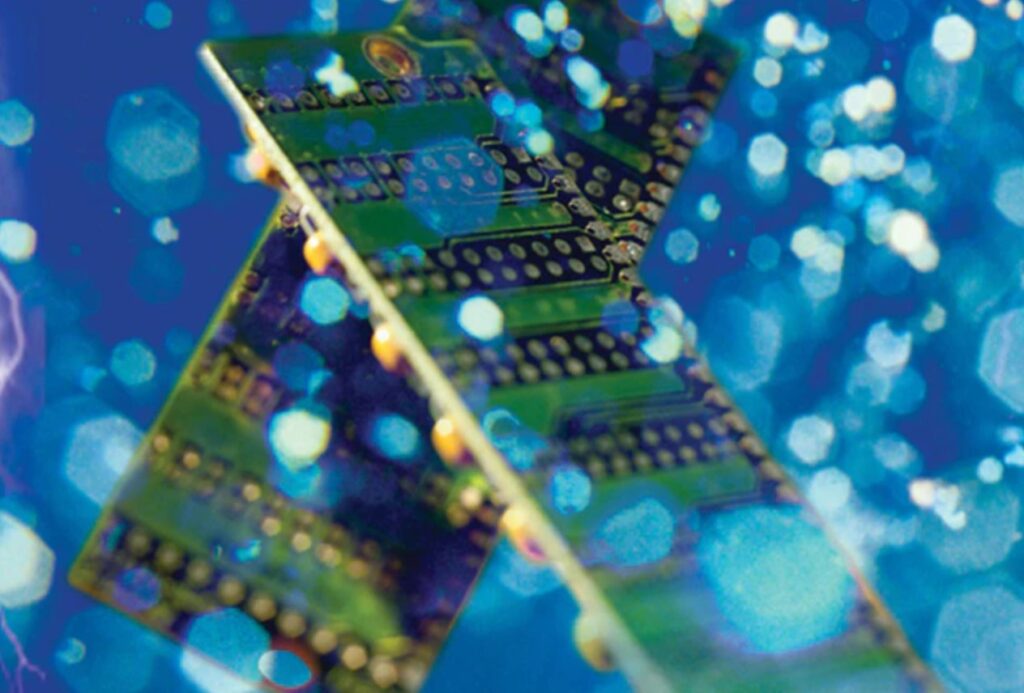
Parylene has proved itself beyond doubt for space use as well. It is the preferred choice of coating on everything from circuit boards to communications equipment. It is also useful in navigation control systems for its insulating properties. The polymer has a high UV and thermal stability and low outgassing making it ideal.
-
Aviation
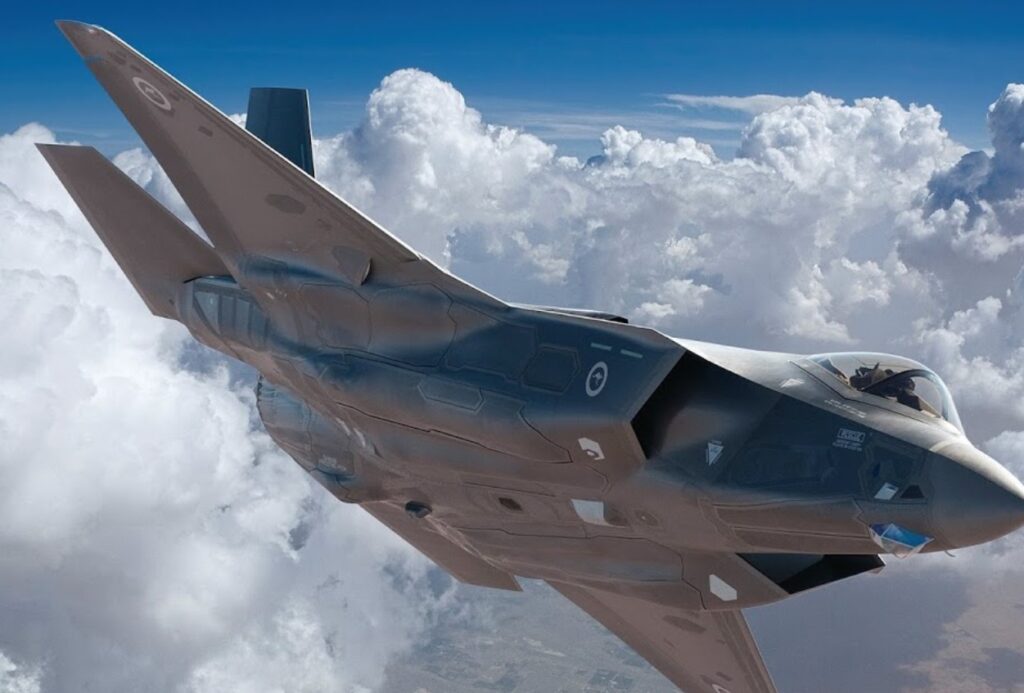
Parylene is useful within the aviation market as well. This is because aviation components are exposed to very harsh environments. The instruments need to work effectively when exposed to UV rays, sub-zero temperatures, range of chemicals and solvents, and moisture. Parylene can help protect cockpit instrumentation, flight control systems, imaging, and display equipment. This makes it the polymer of choice.