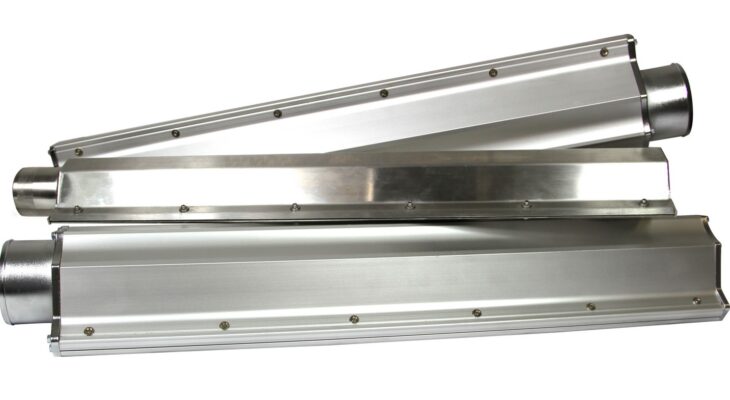
Industrial Use of Air Knife Systems
In the manufacturing or recycling industries, there is a constant need to clean or dry products or parts in the conveyor belt. Pressurized blowers serve this purpose. An air knife system is a tool that discharges pressurized air to blow off debris or liquid from products as they move along a conveyor. They are common in manufacturing or in recursive recycling processes as the first step. In recursive recycling processes, air knives help separate small or light particles from components to be used in later steps. In manufacturing, they help dry parts post manufacture, clean components and clean conveyors.
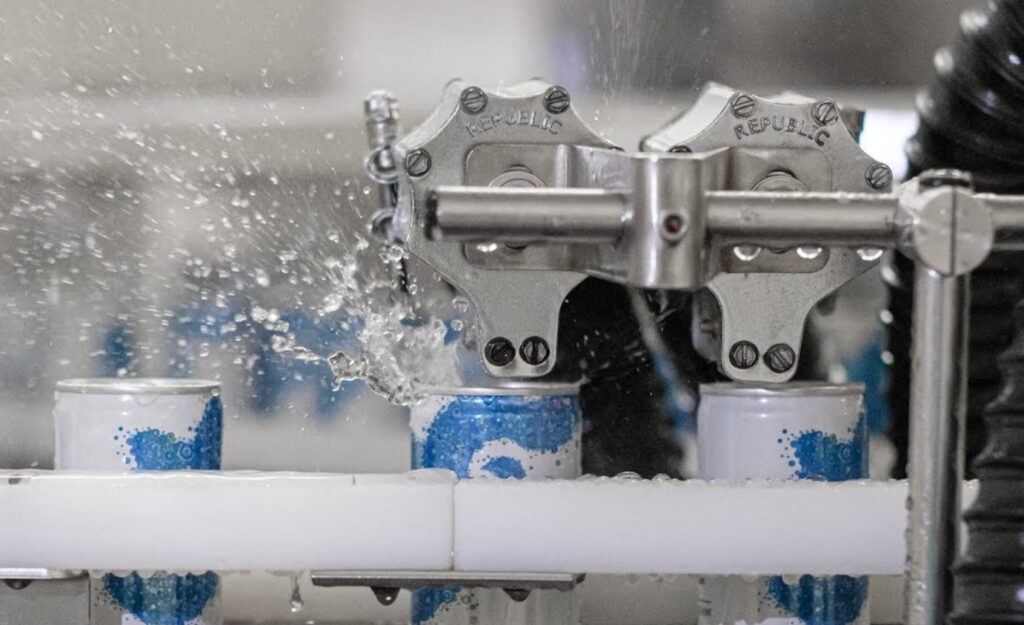
How Air Knife Systems Work
The blower system is one of the best methods of getting rid of unwanted substances from the surfaces of products. There are mobile air knives and stationary ones too. While the mobile ones move over the products or surfaces, the stationary ones work with conveyor belts. The conveyor belt moves the products around as the system blows off any particles from the surface of the products. Despite the slight difference between the two ways air knives can operate, the general setup is the same.
A stationary configuration may involve between 1-12 air knives. The number depends on the application criteria. The air knives in a system vary in size from 0.25 inches to 200 inches. Their discharge also varies between 0.001 inches and 0.25 inches. An air generator, which can be either an industrial blower or air compressor, blasts air through the slots of the air knives.
Air knives can either be powered with blowers or be powered by compressed air. Blower air knives are more efficient compared to compressed air knives. The compressed air knives have connective pipework that delivers pressurized air to the air blower at high speed. The blower then discharges the air to remove debris or liquid from the surface of the product. This is a relatively simple, yet fast and effective process.
The two types have different optimal uses. The choice of the system to use is dependent on several factors. For the compressed air operated air knives, there are several applications to which they can be put. The different applications determine the setup necessary. Compressed air operated air knives are generally ideal for drying, cooling, cleaning and controlling coating. Some of the common applications of this system include:
- Drying of surfaces of parts or products
- Blowing off debris from products or parts with special attention on getting rid of any static electricity on plastic parts
- Controlling coating on parts or products when there is need to spread coating evenly on a part or product
- Drying or setting of parts after coating
- Cooling materials
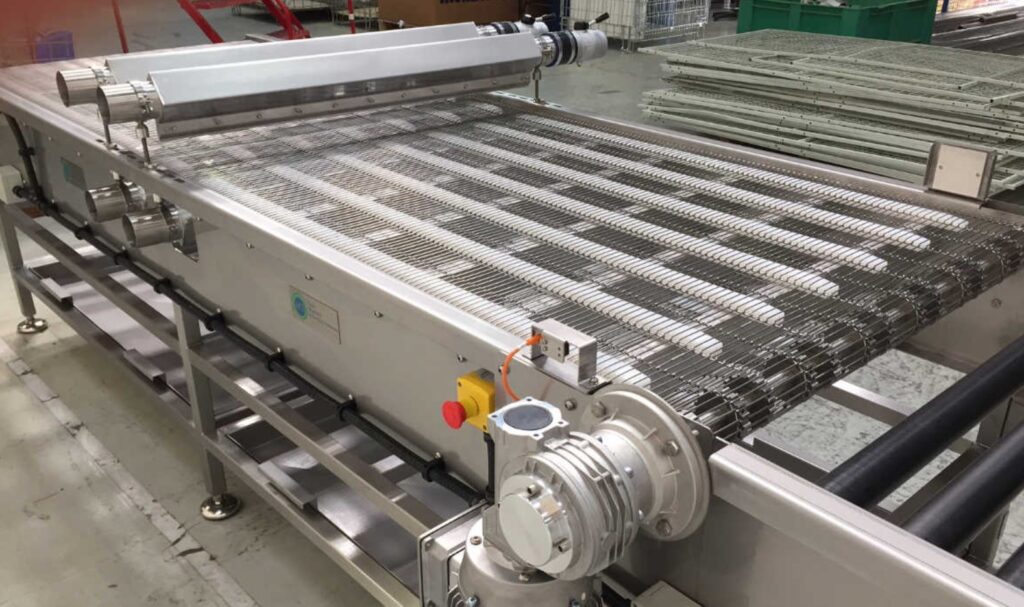
1. Drying of Product Surfaces
The high shear force of compressed air operated air knives makes them ideal for drying especially smooth or flat surfaces. The large blower mass flow and heat from blower systems get rid of any liquid that may be on the surfaces. However, it can leave stains if there were chemical residues on the surface. On the other hand, the compressed air systems are more effective as they have more energy to remove any liquid completely. That minimizes the possibility of stains. The setup of the compressed air system of air knives involves setting the unit flow facing the moving product at about 3 degrees where the system is slow-moving. In a system moving faster, you can increase the angle up to a maximum of 30 degrees. For the amount of pressure, that will depend on the viscosity of the liquid that needs drying as well as the degree of roughness of the surface. More pressure would be necessary for a system involving high speed, high viscosity and high degree of roughness. The input air pressure ranges between 60 and 80 PSIG.
2. Blowing Off Debris
Similar to drying, blowing off debris requires the air knives to be at an angle of between 3 and 30 degrees against the moving target surface. The angle varies depending on the speed of the target surface. While dust can be treated as liquid, larger particles require a different angle setup. Each material needs to be tested against the effectiveness of the angle to ensure the cleaning is effective. The pressure used to clean debris also varies between 30 and 80 PSIG. Very heavy material may necessitate opening up the air gap of the air knives to allow for more force and power. However, that also requires an increase in the amount of compressed air. To clean a statically charged surface such as plastic, an ionizing bar/static eliminator should be attached to the air knives. Pressures of even below 30 PSIG would be sufficient to de-dust statically charged surfaces.
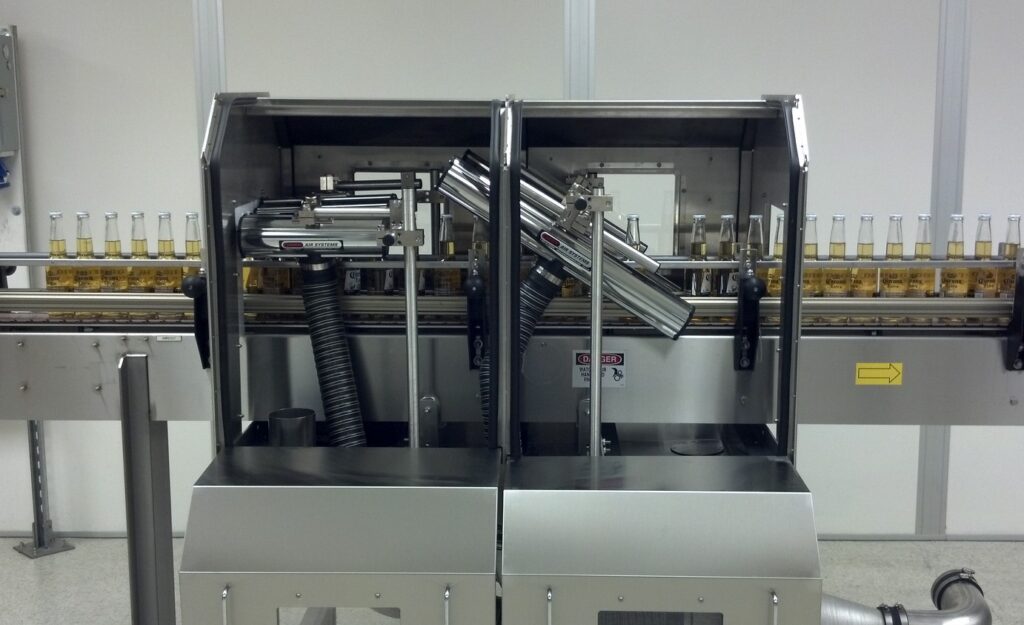
3. Controlling Coating
Controlling the level of coating on a product requires a compressed air knife that has a very sharp edge air flow. According to exair.com, the air knives in this system help spread apply and the coating evenly by controlling the amount of coating through the sharp, even and targeted flow. The depth of the coating required and speed determine the amount of pressure. The viscosity of the fluid is also a determinant of the pressure to be used. Compressed air systems produce laminar flow, which is better in controlling coating than the turbulent flow of blower systems. The air knives for controlling coating are usually at an angle of between 3 and 5 degrees.
4. Drying or Setting of Coating
Air escaping compressed air operated air knives has a cooling effect due to the change in pressure from high pressure to low pressure. The cooling effect helps in drying and setting a coating after it has been applied on a product. The drying and setting helps achieve an even finishing to the coat. The process requires low pressure of between 20 to 30 PSIG. The angle of the air knives should be about 3 degrees against the movement of the material.
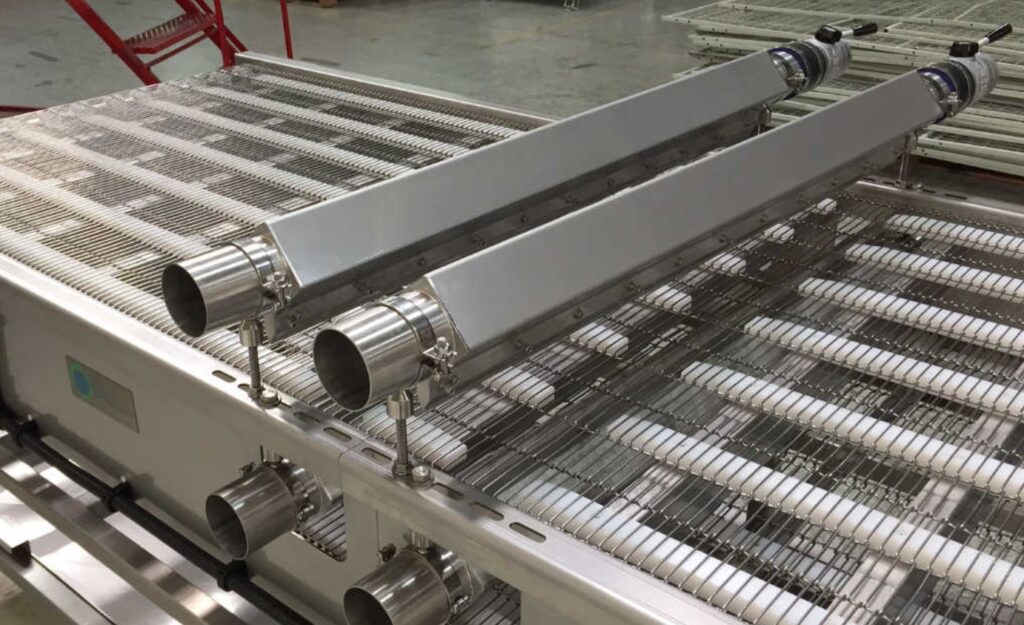
5. Cooling of Material
The cooling effect of air escaping from compressed air systems is important for cooling. Additionally, a high velocity from a compressed air system results in the cutting of the boundary layer produced due to heat in a hot target, causing a cooling effect. The laminar flow also adds to the cooling effect. The three combine to produce a cooling effect that helps in cooling material. The amount of time it takes to cool a given substance depends on several factors. If the temperature of the material was high, it would cool faster, but the rate of cooling reduces as it gets cooler. For effective cooling, it is important to maintain a slow speed. Alternatively, using multiple air knives can help cool the product faster. The angle of the air knives should be about 3 degrees while the pressure should be 80 PSIG to allow for optimum mass flow and velocity for effective cooling.
Despite the differences in application, air knives are an ideal method of drying, cleaning, cooling, controlling coating, and setting coating on surfaces of products or material in industrial settings. They are economical and efficient. They use pressurized air to create an impact velocity upon exit from the air knives to cause different effects on the target surfaces. The amount of pressure varies from one application to the other. Similarly, the angle of the air knives and the speed of the target products on the conveyor belt varies depending on the application or the material to be cooled, dried or cleaned.