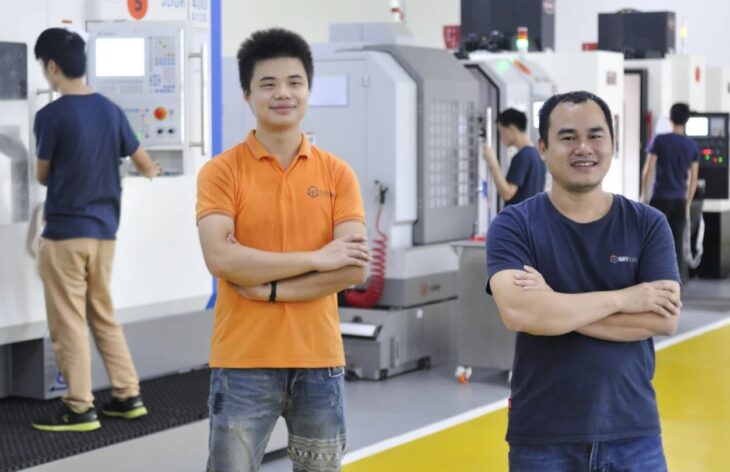
Industry 4.0 Has Encouraged CNC Production Growth in the Rapid Prototyping Industry
Nobody wants to let their machine shops fall behind in the technology development of this era. WayKen Rapid Manufacturing is an innovative company and committed to embracing the new tech and knowledge so that they can get an edge in the fierce competition. This is an article from their points about how industry 4.0 changed the CNC production in the rapid prototyping industry.
1. CNC Machine Shop Prepares For Industry 4.0
According to Klaus Schwab, a German economist suggested that interconnectivity would drive the future of the industry, which also refers to the fourth major industrial revolution. Human society has been through 3 industrial revolutions, the first used steam, and water power to operate machines, the human being has entered the power industry times after the second, and the factories of what many call the third industrial revolution will become from BIG to SMART. Digital manufacturing is the key feature of Industry 4.0, IoT would integrate factories and services, data would be collected automatically.
2. Four Aspects of CNC Machine Tools Affected By Industry 4.0
When conventional manufacturing technology is not reliable, the quality is not stable, it always causes downtime to find out the reason, and increases costs.
Non-stop operation — It’s very important to eliminate downtime as little as possible. When the CNC machine shop needs to shut down for some reason, how much cost would occur, the production, labor and maintenance fees. Imagine a shop produces 800 units per hour at an average profit of $100, just one hour of downtime would cause $20,000 in revenue. With a robust stream of performance and real-time data, industry 4.0 allows an entirely new opportunity in the form of preventive maintenance. Big Data solutions make it even possible to build the models to identify potential failure points, many of which otherwise may not obvious to the naked eye.
Energy savings — It’s known that machine tools and hardware are energy hogs, even when they’re just standby, resource and energy can be better managed with the help of Industry 4.0 solutions. The whole system can be automated by setting up motion alerts and maybe a human presence to detect when they should be on or off.
Improved Quality assurance — Industry 4.0 related technologies allow real-time QA, data is collected about the machine performance, quality, and state of goods, problems get addressed immediately. When equipment has some issue, loses its efficiency or is just plain inaccurate, the processing goods suffer as a result. That’s why CNC production always has a quality assurance process in place to inspect the goods or components. Without sending your finished products offsite for inspection, sensors could do it in your shop.
Better human-machine coordinate – Many workers stay alongside the robots and machines day-to-day refer to as cobots, the future machine shop will improve the iteration of humans, machines and manufacturing, the factory floor will be an extremely efficient, more smooth, and safer environment. To get there, however, the user interface needs to be significantly improved. Engineers will be able to remotely control equipment, reporting systems will provide real-time alerts and insights to operators.
All these lead to decrease downtime, machines operates continuously, less failure, quicker turnarounds and at more efficient levels than ever before.
3. How New Technology Will Change CNC Production Processes
Today, even many CNC machine shops are equipped with computer-aided manufacturing software, with the development of 5G, many CNC machine shops still work under unconnected, they are not able to download the latest programs or specifications.
Connect computers with internet in the CNC machine shops can make the machines more precise, which also means sharing information with entities outside the CNC machine shop. This is relatively a new way throughout the whole product life circle. The experts outside the shop can consult on your projects remotely. Furthermore, you can stay close with the institutes creating the latest technology for Industry 4.0. It gives you the opportunity to provide you what technology the machine shop needs.
Companies such as Siemens, PTC are dedicate to integrate software platforms linking all kinds of manufacturing, from the very beginning part design to factory layout to customer feedback after delivery. This “digital thread” makes data exchange happen between incompatible systems, it brings 3D CAD modeling, visualization tools, DFM (design for manufacturing), CAM (computer-aided manufacturing), CIM (computer-integrated manufacturing), and shop floor data collection systems altogether.
Using sensors to track your machine shop’s tools and hardware can also determine the amount of energy used. This kind of information leads to better decisions, you can automate the system to become more energy efficient. It not only help you to increase productivity, but also reduce energy expenditures. Sensors also gather information about machine performance, problems get addressed immediately, downtime decreases.
4. How We Can Help Clients?
We often have clients that come to us after working with others on a project, the misunderstanding, low accuracy, defective surfaces, unsatisfactory after-sales service….The engineers are frustrated because of the time and money they have already invested and yet are not happy with the result. With 20+ years’ experience, Wayken offers the solutions for you.