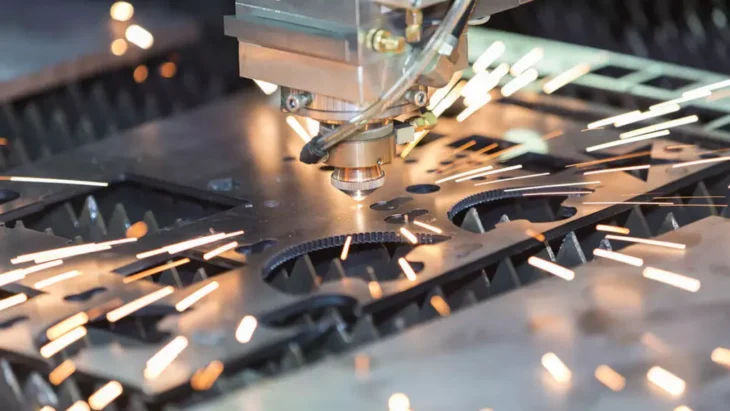
How Accurate Are Laser Cutting Machines – 2024 Guide
Materials must be sliced for surface microstructural changes to take place. Laser cutting is one of the popular methods for machining materials.
It is beneficial to develop patterns in accordance with designs and desired results. In this procedure, materials are heated, burned, and vaporized in the presence of an intense laser beam.
A laser cutter, which focuses a tiny laser beam on the material, allows for the successful cutting of materials.
Materials can be etched more efficiently than ever before with laser cutting. These days, users may quickly and accurately cut through any material, be it metal, wood, or another one. To the cutting machine these have sparked a revolution.
The accuracy of laser cutting devices will be the main topic of today’s article.
What is Laser Cutting?
In the fabrication process known as laser cutting, the material is sliced into specific shapes and patterns using a concentrated, powerful radiation beam. This method can create precise, elaborate, and complex pieces without the requirement for specially designed tooling and is applicable for various materials, including metal, plastic, wood, glass, and paper.
The fact that this technology is now the most affordable cutting alternative and is developing is one of the factors contributing to its widespread use. The quality and efficiency of material cutting are improved by numerous advancements in laser technology. The three fundamental approaches of this methodology are now well known. These are: through melting, through oxygen, and through evaporation.
How Accurate is Laser Cutting?
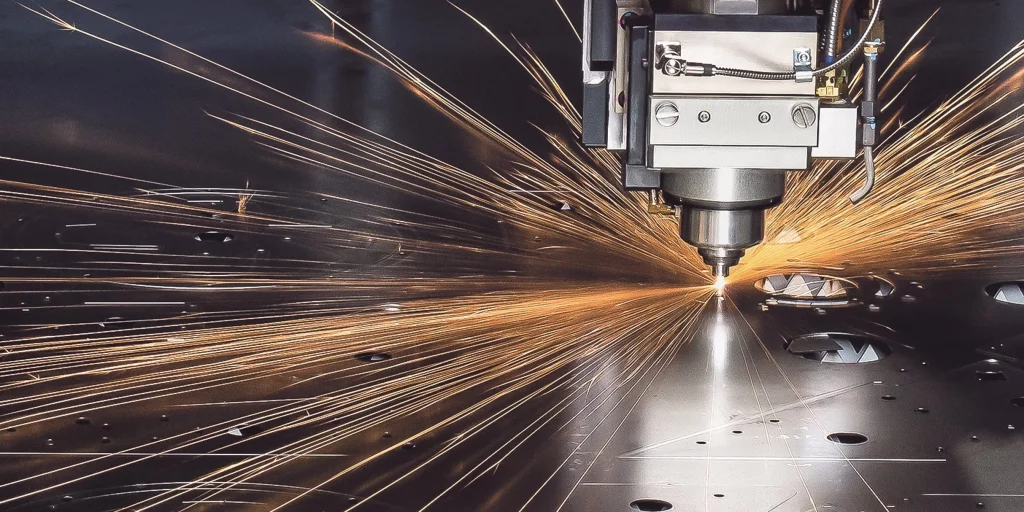
Compared to other conventional sheet metal etching procedures, this type of metal etching is a highly effective, secure, and accurate technology. A computer-driven program is used in the laser cutting procedure to precisely cut materials with tolerable accuracy.
CAD software can be used to direct the beam as it makes its cuts as part of this process. A 25-micron target, or roughly 14 of the width of a human hair strand, is the ideal size for laser cutting. More so than 0.001 inches, the cut width might also be relatively small. On the other hand, the dimensional precision is often very accurate, at 0.0005 inches.
Metaletching offers clients in a variety of demanding industries laser cutting services.
Advantages of Laser Cutting Machines
Compared to other metal cutting techniques, this type of cutting offers significant advantages since it has the power and precision to enable organizations to achieve outcomes on a never-before-seen scale. Laser cutting is a field that is constantly evolving; therefore, as it expands, it only offers more advantages. With the most recent technologies, you may receive the best cut at the fastest speeds and lowest cost.
- High-Level Precision And Quality
High accuracy and nature, or high quality of the cut material, are two guiding characteristics of this etching method. The accuracy has been improved thanks to the development of CNC technology and the enhancement of the beam shaper head. In addition to great accuracy, the benefit is related to the slicing time, which is gradually reduced.
Several laser cutting devices have multi-axis layers. They may cut various unique styles and shapes thanks to this process. Additionally, they can cut materials of many shapes and sizes, including alloys and other metals. Even the most intricate constructions can be easily sliced by these devices.
Laser cutters are capable of processing many materials at once and may produce intricate forms in a range of materials. Due to these qualities, laser cutting is able to create practically any form of pattern.
- Automation
Due to the excellent level of automation in modern laser cutting equipment, the job requires little human labor. While an expert machine operator still contributes significantly to the end product’s quality, the speed of slicing and minimal requirement for manual work lead to cheaper costs than those associated with other etching techniques. Many machines even include feeding mechanisms and subsequent conveyors. Of course, such configurations result in a more expensive laser cutting machine.
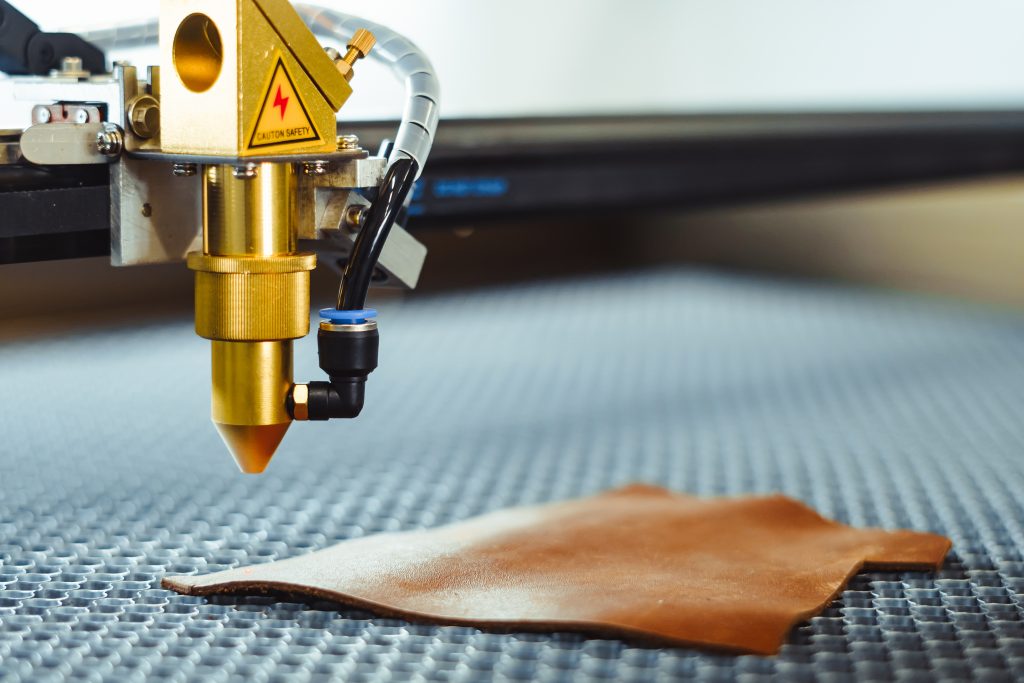
- Affordable
One of the benefits of this technology is the cost advantage it has over other CNC machines of the same class. With the use of laser cutting technology, no special tools are required. The device does not require modification for any project because no additional cutting tools are needed.
Since there is no physical contact, the surface does not deteriorate either. Since the mechanical parts of the laser cutter are few in number, maintenance is less expensive than with other machining techniques. In comparison to conventional manufacturing tools, the machine’s operational costs are also lower.
- Damage Minimization
Laser cutting also has the benefit of protecting even the thinnest materials from damage. Many people have a tendency to accept false information regarding the technology, such as the idea that materials will inevitably bend or become damaged. According to a common misconception, significant heat is used during the laser cutting process. It’s important to note that heat only affects a small portion of the material and has no impact on tolerance. Slicing takes less time because the beam cuts through sheets at rapid speed. As a result, producers can easily steer clear of distortion and warping.
- Utilizes Less Energy
While energy is still needed, laser cutting is thought to be more energy-efficient than many other cutting techniques. It makes etching procedures quick and straightforward for manufacturing organizations. This process often uses less energy than conventional cutting techniques due to the rapid slicing speeds it operates at.
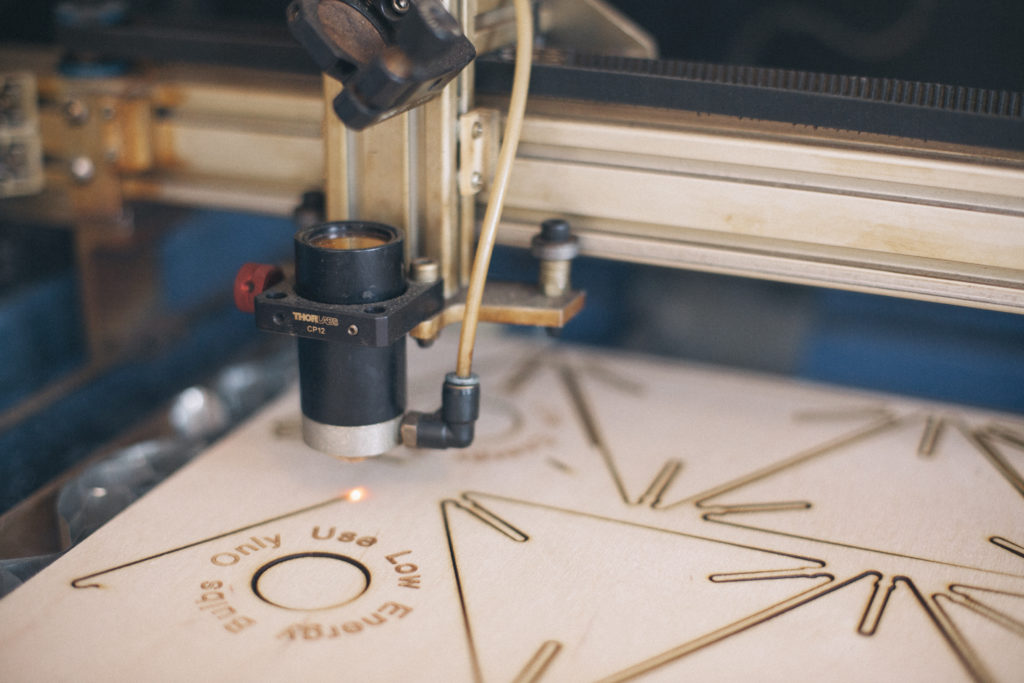
Conclusion
In today’s industry, the value of this kind of technology and equipment is enormous. In addition to assisting us in positive actions, it also helps us avoid wasting time and, eventually, money. The majority of laser processing equipment uses CNC control.
The use of 2D and 3D etching technologies are standard since they are highly advanced machining techniques. The processing of vehicle bodies, the aerospace sector, and the slicing of specialty materials like aluminum, chromium, etc., all make use of this technology. The processing of non-metals using laser cutting machines will expand the scope of this technology’s application.