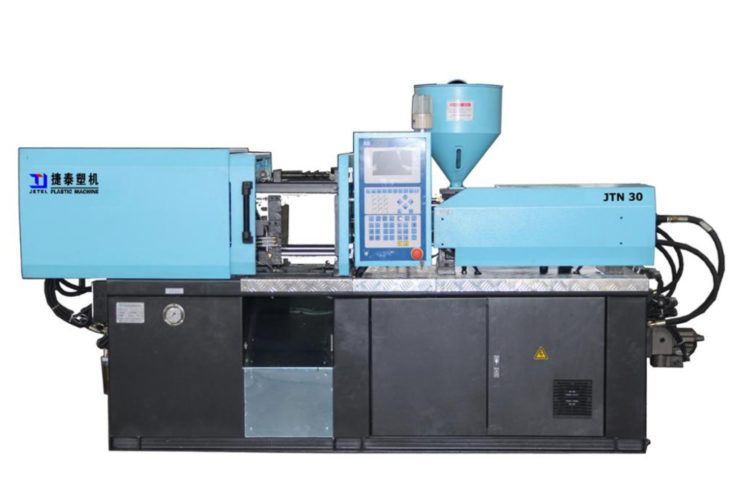
Types of Injection Molding Machines
Each and every person on this earth use plastic items every day in their lives. From plastic bottles and plastic chairs to musical instruments and utensils, there is no denying that these objects are present in each household. However, what do you really know about the manufacturing processes of these items? Do you know anything about injection molding?
If you are wondering where the most common items in your household came from, you might find this article to be quite helpful. The text below is going to feature the different machines used for injection molding processes, however, before we take a look at that, let’s first take a look at what exactly are these devices, and how do they work.
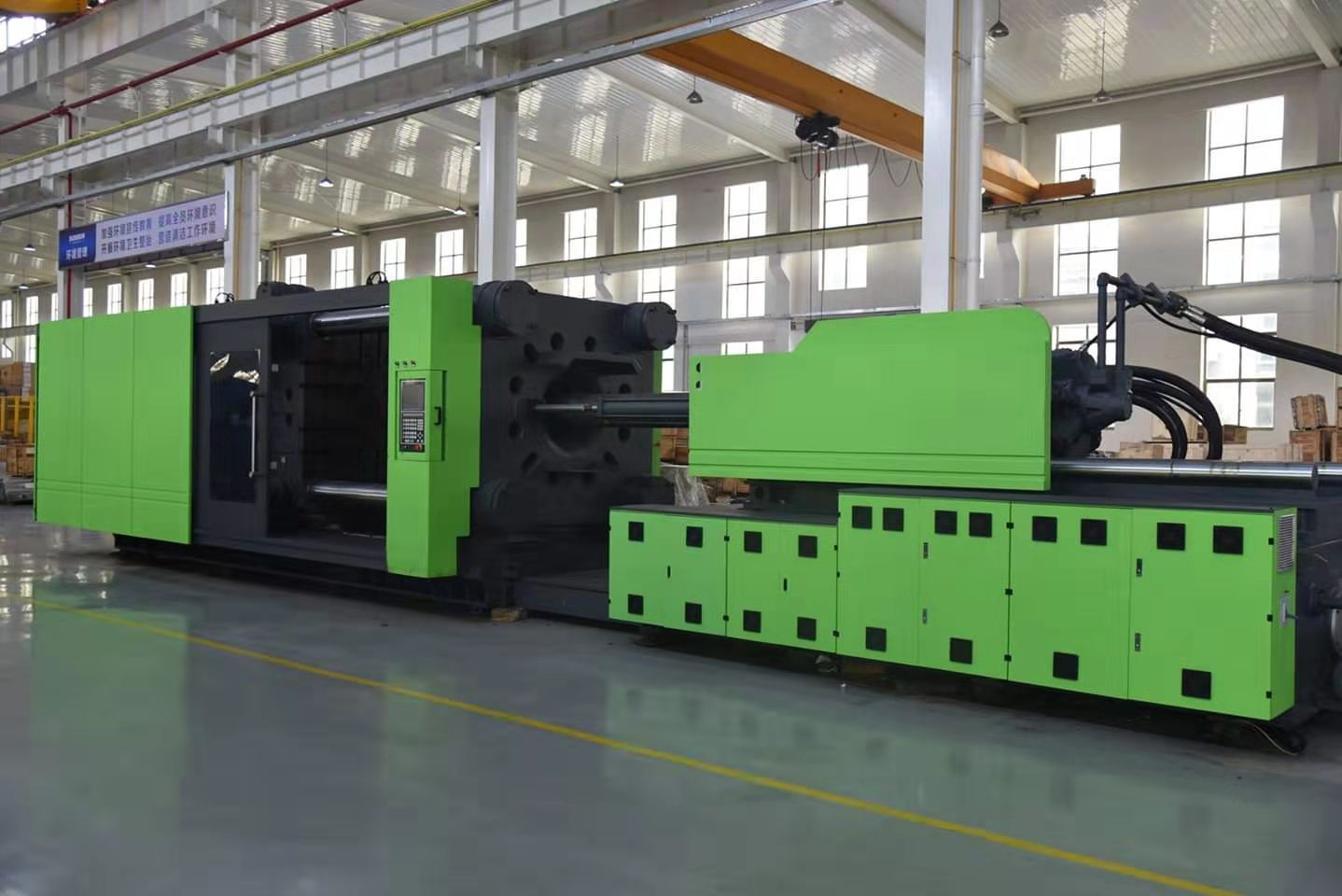
What Are Injection Molding Machines & How Do They Work?
The first thing you should know about these injection casting devices is that they are complex pieces of machinery that are used for mass manufacturing of solid parts by utilizing injecting molten materials by a tube screw system into a cast. Generally speaking, there are a lot of parts that make these instruments work including a hopper, barrel, a system that controls the temperatures, as well as the cast itself.
The process is quite simple to understand – raw materials such as metal or plastic are placed inside the barrel, and it is then subjected to high temperatures or pressure that melts the material. Next, the barrel turns the screws inside of it, and in return, it injects a specific amount of the melted material inside the cavity. Once it is properly fitted with the material, the devices turn off.
The compartment holding the material is then cooled down until it is ready to be taken out of it. This can, of course, take some time and it will mostly depend on the materials inside of the cast, as well as the size, shape, and thickness of the part that is being mass-produced. Once cooled down, the device will open automatically.
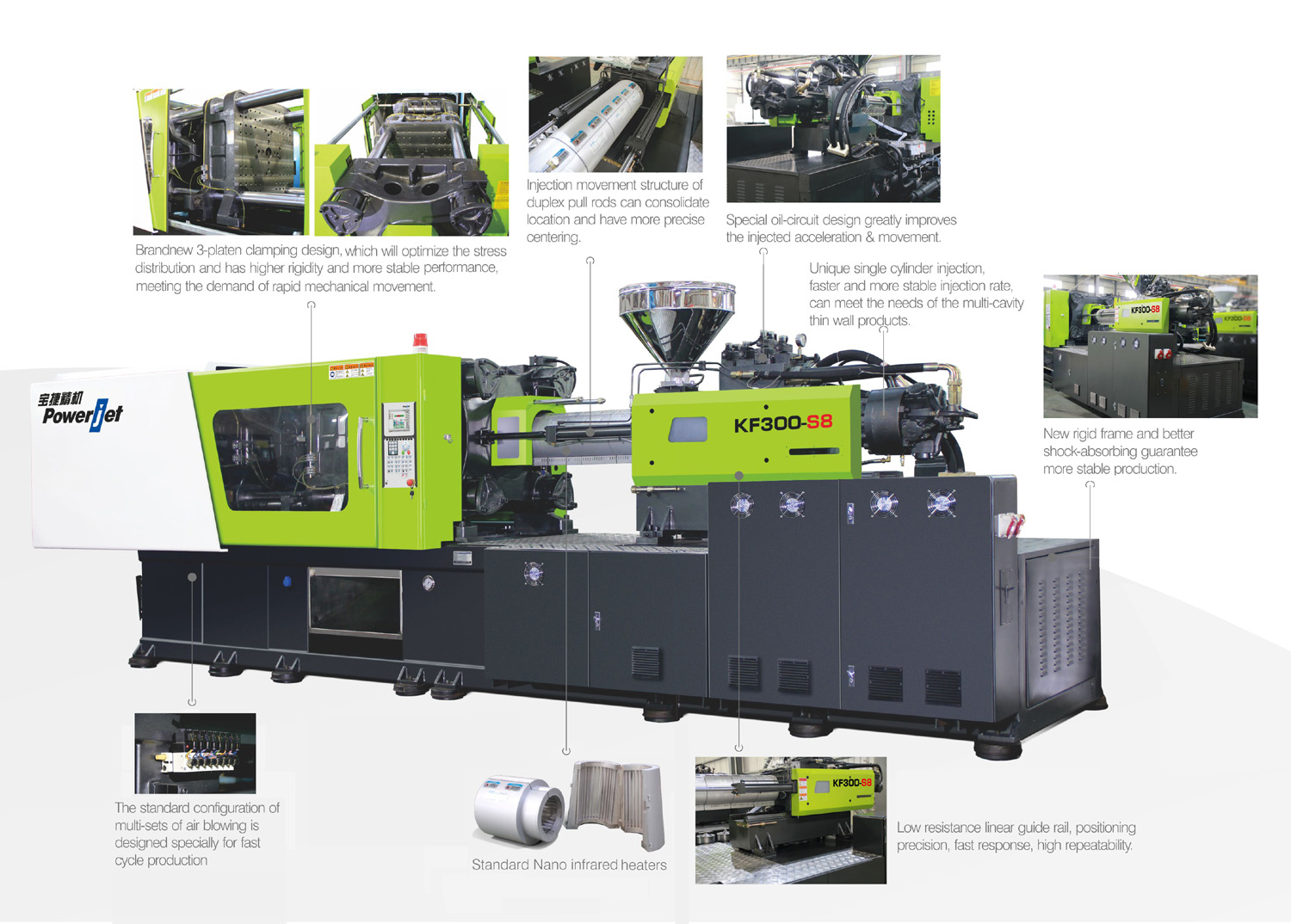
The Four Most Common Injection Molding Types
These complex electrical tools are categorized mostly by the type of system that they use. The four most common types include:
- Hydraulic Devices
Historically speaking, this type was the first and only option for manufacturers back in the day – that is until Nissei, a plastic manufacturing company presented the first-ever all-electric press during 1983. Although they are not as precise as the other devices on this list, they are still most commonly used all over the world, except for Japan.
- Mechanical Devices
Now, the mechanical alternative utilizes a toggle system for increasing the tonnage on the clamp side of the device. Of course, tonnage is needed on all types in order for the clamp side to remain closed due to the pressure the injection produces. If the devices decided to open up during the production process, it would create an error in the plastic components.
- Electric Devices
The electric ones are probably the most commonly used type, especially since it can easily lower the costs of production by lowering energy consumption. Besides that, it is considered to be quite environmentally friendly. They also work quicker, quieter, and they are extremely accurate. If you are interested in learning more about these useful tools, check out Qmolding for additional information.
- Hybrid Devices
Hybrid devices can provide more benefits and advantages to the manufacturer, especially because they incorporate all the advantages of the previously mentioned types. It even uses the same level of electricity as the electric ones, which means that they can also lower the costs of production.
Although it is not really a specific type, it is still worth mentioning – these presses need the help of a robotic arm. This “arm” needs to be implemented in order for it to remove the formed parts either by entering from the side or from the top. However, a lot of manufacturers prefer if their products drop from the shell into the robotic arm’s container.
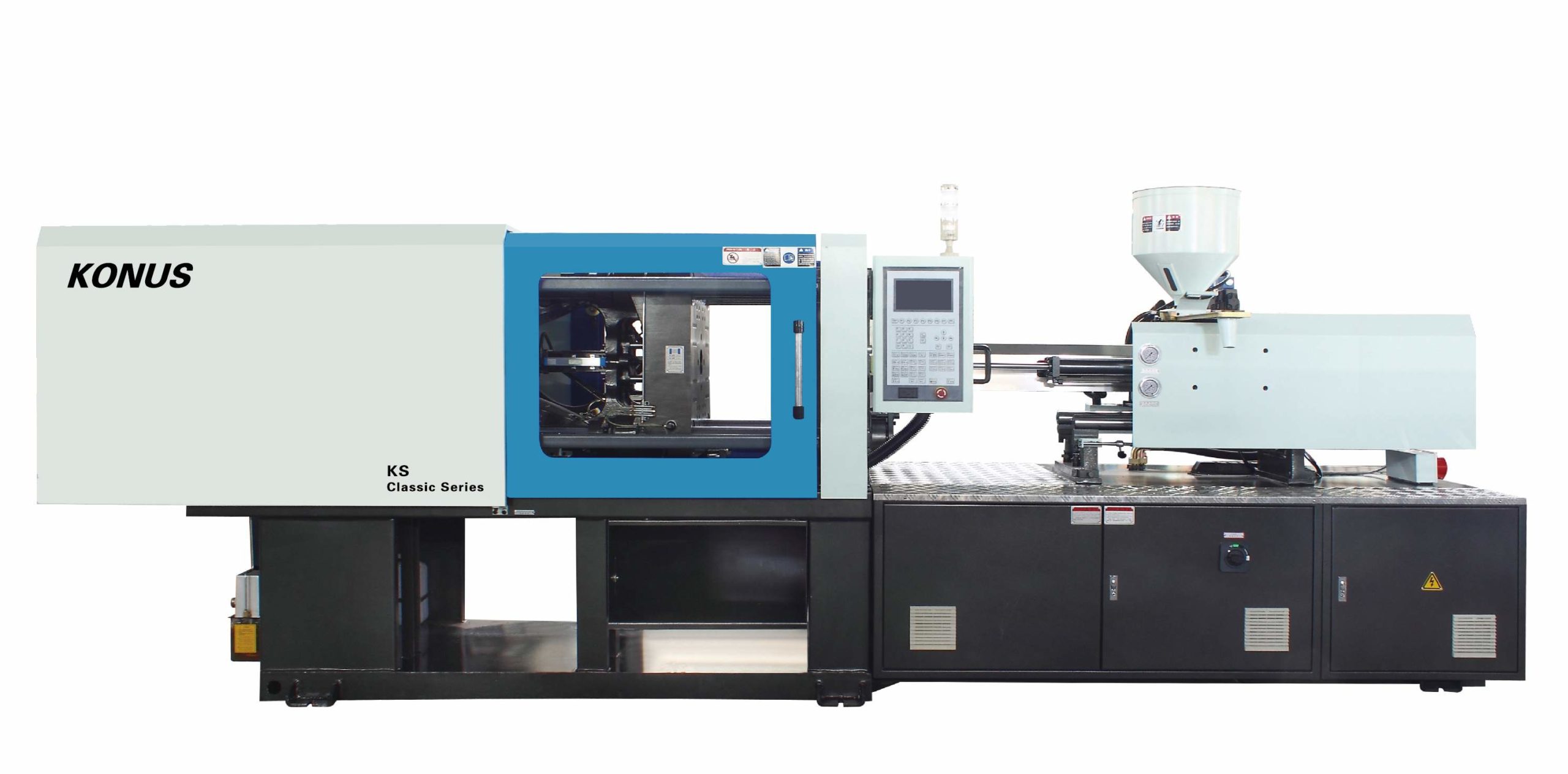
What Are The Advantages of Utilizing These Devices?
There is a wide range of benefits and advantages that these devices can bring you, including:
- Low Waste – when you first purchase it, you’ll probably need to use some plastic materials in order to calibrate it properly – and the materials will be unusable in the future, meaning that you should throw them away. However, once you are done with calibrating it, the machine will produce a minimal amount of waste, which means that they are quite efficient and precise.
- Repeatable Production – the processes done by these machines are repeatable, hence, you can create the same plastic component hundreds, thousands, and even millions of times! So, your production plant can create the necessary component over the course of a few years without losing efficiency or consistency.
- The Color And Resin Options Are Endless – there are millions of colors and resins that you can choose from, which means that your products can be quite diverse. Besides these endless options, you can also opt for having different inlays and overmolds that will allow your products to have specific finishes and designs that could not be available in other manufacturing processed.
- The Molds Can Make Several Components At Once – the molds featured on these devices can actually create several components at once. So, if you need 5 of one component and 3 of another, one mold can actually produce all the parts in one try. This means that you can cut production time, which of course, leads to a lower production cost.
Conclusion
As you can see, injection molding machine is used and implemented in manufacturing plants all over the world. Naturally, you can opt for purchasing a machine of your own, however, if you do not need it all the time, you might also want to consider hiring a company that will produce the plastic or metal components that you need.
So, now that you know everything there is about these machines, you should really not lose any more time. Instead, you should start thinking about what machine or services you should opt for right away!